Challenge
The top management vision at Notthoff is to double the company’s sales in the next 3 to 5 years. To grow, Notthoff needed to improve customer satisfaction by improving on time delivery and quality. To accomplish these objectives, it is critical that the company reduce lead times, reduce work-inprocess, improve on time delivery and increase capacity. It is also critical that equipment set-up time be reduced and downtime minimized, if not eliminated.Solution
To assist Notthoff learn and apply methods to reduce waste in their set up processes, a Lean manufacturing program to train and facilitate implementation was initiated in March 2008. Notthoff’s team focused on the concepts of 5S for organization and Single Minute Exchange of Die (“SMED”) to reduce setup time. Training was conducted on basic Lean principles and 5S methods to identify and remove waste in two key pilot production areas. Current set up processes were then analyzed and the team brainstormed on how to reduce process waste and shorten the time between the “last good part produced” and the “first good part produced” on the next job. 5S also helped to decrease equipment downtime by improving machine cleanliness and exposing equipment problems. The project ended in late May 2008.
Improvement Description
The results of the project dramatically improved the organization and cleanliness of the shop floor. Notthoff team members applied 5S not only in the two pilot areas, but also in other areas. The SMED activities proved to the team that as much as a 50% reduction in set-up times could be achieved and would result in significant increase in capacity and cost savings.
Financial and Investment Impact
Notthoff estimates that with sustained improvements spread throughout the facility, the cost savings could be as much as $500,000. The project provided the capacity to handle an additional $4 million in sales over the next 3 years.
"To stay competitive in this industry you need to be Lean and mean. CMTC helped us with the Lean part."
Terry Kaller
President![]()
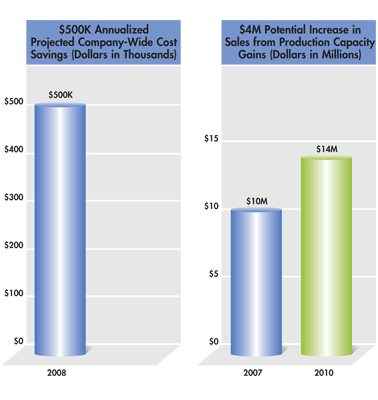
Case Studies
- Additive Manufacturing (3)
- Aerospace and Defense (14)
- Apparel (3)
- Business Growth Strategy & Strategic Planning (27)
- Continuous Improvement (7)
- Employee Training (13)
- Energy (7)
- Exporting (4)
- Farming (1)
- Food and Beverage (16)
- Fourth Industrial Revolution (24)
- Health & Safety Services (2)
- Industrial (1)
- Information Technology (3)
- Innovation & Growth (17)
- Lean (34)
- Machinery (1)
- Made in California (7)
- Manufacturing Technology (3)
- Plastics and Rubber (1)
- Quality (27)
- Sales and Marketing (32)
- Smart Manufacturing (1)
- Supply Chain Management (1)
- Wood (1)