Food Makers Bakery Equipment is a family-owned business that has been serving the baking industry for more than 30 years. The company manufactures a variety of fabricated goods and equipment parts. The company offers a range of equipment and has 47 employees who are located in Irwindale, CA.
Challenge
The organization was challenged by delays during the production process, particularly for their popular baker racks and tables. This was impacting their client retention efforts. They also wanted to decrease lead times, improve their efficiencies, and reduce operational costs so that they could become more competitive in the market for new customers.
Solution
The owners of the company connected with CMTC. After an initial evaluation of needs, it was determined that a Lean Transformation Program would address the organization’s challenges. This program utilizes various Lean tools and training to identify weaknesses and improve operational performance. A Lean 101 Awareness Training session introduced key managers and employees to Lean principles.
Value Stream Mapping (VSM) was used to create a visual representation of the company’s current state of its production conditions and an improvement plan for the desired future state of its production conditions. A Kaizen event was conducted on their key production lines for baker racks and tables to identify and eliminate excess costs and delays during the production process. 5S training coached employees on how to reduce clutter and keep the workplace more organized to enable a more efficient and smoother production process. Employees were given recommendations on how they could reorganize equipment on the production floor, which would enable them to improve the flow of operations, and eliminate unnecessary equipment and supplies. Managers were also trained on how to sustain the improvements.
“CMTC’s Lean Enterprise Program enabled us to become more efficient. Our improved operational performance resulted in a 10% increase in new sales and a 3% decrease in expenses.”
- Tom and Linda Fowler, Owners![]()
$237,000 in Capital Investments
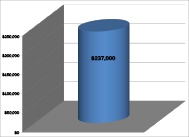
5 Jobs Retained
Financial & Productivity Results
- 10% in increased sales
- 5% in retained sales
- 3% in cost savings
- 5 jobs retained
- $237,000 in capital investments
Case Studies
- Additive Manufacturing (3)
- Aerospace and Defense (14)
- Apparel (3)
- Business Growth Strategy & Strategic Planning (28)
- Continuous Improvement (8)
- Employee Training (14)
- Energy (7)
- Exporting (4)
- Farming (1)
- Food and Beverage (16)
- Fourth Industrial Revolution (24)
- Health & Safety Services (3)
- Industrial (1)
- Information Technology (3)
- Innovation & Growth (17)
- Lean (35)
- Machinery (1)
- Made in California (7)
- Manufacturing Technology (3)
- Medical (1)
- Plastics and Rubber (1)
- Quality (27)
- Sales and Marketing (32)
- Smart Manufacturing (1)
- Supply Chain Management (1)
- Wood (1)