Challenge
In 2005, CMTC® conducted an assessment to determine cost improvement areas in the Komyo distribution center. 10 areas were identified. To improve competitiveness and position the company to acquire new business, Komyo management chose to address all 10 areas. Komyo contracted with CMTC to address opportunities in the areas of Container Logistics, Crossdock Receiving & Shipping Operations, “In-house” Warehouse Operations, “Dealer” Order Processing, Inventory Control Operations, Headcount Analysis, Operational Finance Review, Information Systems Review, Security Review and Management/Supervisor Assessments. The project was completed in 2006.
Solution
Reviews were conducted with site managers throughout the Chino distribution center using process improvement and Value Stream Mapping tools. Following this phase, mentoring of employees and “hands-on” guidance in the various techniques necessary to support improvement within the center were implemented. Employees continuously modified the original solution for the precise fit to the specific departmental and center requirements. Mentoring continued onsite for 6 months, allowing Komyo management to focus on the day-to-day operations and continue to develop the skills to move the business forward. All new processes were documented to preserve the knowledge from the project for potential future use at new Honda site operations. Additional information systems projects and management/supervisor training programs established new processes that allowed Komyo team members to proactively identify and resolve issues before they had an impact on Honda USA and its customers.
Improvement Description
The project provided several benefits. It achieved a 40% operational improvement goal and moved Komyo from a “middle of the pack” to a “best in all categories” company in six months. The project also became a catalyst for Komyo to earn the opportunity to develop additional Honda USA Logistics sites. Improvements in the Crossdock operations have eliminated the backlog of incoming containers. Process improvements in the “Dealer” processing, Inventory Control and Information Systems have all contributed to an overall lead time reduction of 6 days to the end user. Reduction in overtime hours netted significant annual labor savings. While overtime was being decreased, volume was on the rise which led to an increase in Komyo’s most important performance measure: Lines per Man-hour. Inventory accuracy also increased.
Financial and Investment Impact
Komyo’s total revenues increased by approximately $30 million annually. Additionally, Komyo increased productivity by 262%, saving $3.3 million annually. Inventory accuracy increased from approximately 90% to 99.9999%.
"We needed improvement now! CMTC exceeded our expectations."
Richard Franklin
Director of Logistics![]()
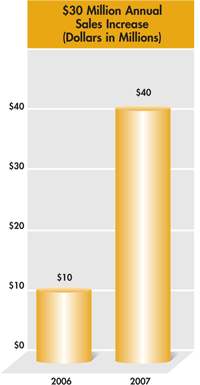
Case Studies
- Additive Manufacturing (3)
- Aerospace and Defense (14)
- Apparel (3)
- Business Growth Strategy & Strategic Planning (28)
- Continuous Improvement (8)
- Employee Training (14)
- Energy (7)
- Exporting (4)
- Farming (1)
- Food and Beverage (16)
- Fourth Industrial Revolution (24)
- Health & Safety Services (3)
- Industrial (1)
- Information Technology (3)
- Innovation & Growth (17)
- Lean (35)
- Machinery (1)
- Made in California (7)
- Manufacturing Technology (3)
- Medical (1)
- Plastics and Rubber (1)
- Quality (27)
- Sales and Marketing (32)
- Smart Manufacturing (1)
- Supply Chain Management (1)
- Wood (1)