Challenge
Marineland faced increasing competition in the consumer products segment of their business. Their executive management sought to reduce their costs by transferring the production of their power filter product family to offshore contractors in China. The VP of Operations, having already embraced Lean “thinking,” convinced his executive management that Lean “thinking” was the right direction for the company to pursue first to see if sufficient savings can be realized to avoid transferring this product to China. There were several significant issues (e.g. payment terms, increased lead times, quality problems, increased inventory exposure, reduced flexibility to change and the inability to adjust to unexpected swings in demand) associated in moving the production offshore that would be avoided if the manufacturing was to remain in their Moorpark, CA facility.Solution
CMTC®, who previously provided Lean training to both the entire executive management staff and a Lean implementation team of 20, was again contracted, this time to facilitate a Kaizen Blitz on the power filter manufacturing operation. A Kaizen Blitz is an intense Lean implementation activity project in which team members apply Lean principles and tools to make rapid improvements in a process. CMTC utilized the California Employment Training Panel (ETP) funding to offset a portion of Marineland’s training costs. Over a four day period during the second week of April 2004, the team conducted and completed their 4-day Kaizen Blitz.
Improvement Description
The 4-day Kaizen incorporated the following Lean principles and tools: 5S’s of Workplace Organization, Kanban visual signals to trigger work flow, Point-Of-Use-Storage (placing all required inventory close at hand), set-up of sub-assembly Supermarkets, the re-layout and movement of manufacturing equipment into workcells, initiation of single-piece flow in workcells, establishment of visual work instructions, posting of hourly status boards with metrics and the retraining of production personnel. In addition, some quality issues were resolved and supplier price concessions were negotiated. The resulting benefits included: a 27% increase in labor efficiency, a 59% reduction in changeover time between power filter models, a 75% reduction in employee travel time and an overall cost reduction of 10%.
Financial and Investment Impact
On the afternoon of the fourth day of the Kaizen Blitz event, the team presented their accomplishments to executive management. The Kaizen Blitz resulted in an annualized reduction in labor costs of $106,000 and $49,000 per year in supplier price concessions. The greatest impact, however, was Marineland’s decision to retain the manufacturing of the power filters in Moorpark, CA and not send it offshore to China. This resulted in the retention of 13 Marineland employees.
"The bottom line is that this project put off, at least for the time being, the movement of manufacturing jobs from California to China."
Gary Smith
VP![]()
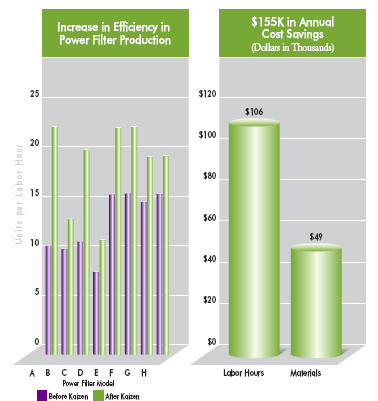
Case Studies
- Additive Manufacturing (3)
- Aerospace and Defense (14)
- Apparel (3)
- Business Growth Strategy & Strategic Planning (28)
- Continuous Improvement (8)
- Employee Training (14)
- Energy (7)
- Exporting (4)
- Farming (1)
- Food and Beverage (16)
- Fourth Industrial Revolution (24)
- Health & Safety Services (3)
- Industrial (1)
- Information Technology (3)
- Innovation & Growth (17)
- Lean (35)
- Machinery (1)
- Made in California (7)
- Manufacturing Technology (3)
- Medical (1)
- Plastics and Rubber (1)
- Quality (27)
- Sales and Marketing (32)
- Smart Manufacturing (1)
- Supply Chain Management (1)
- Wood (1)