Challenge
MCA Tile was experiencing a very high order backlog for theirproducts due to the increased demand for housing throughout the U.S. This prompted MCA Tile to look for ways to increase their daily output by improving quality and productivity in order to continue to provide service to their customers.Solution
In October, 2005, and lasting five months, MCA Tile and CMTC worked together to identify areas for energy savings, improved quality and increased productivity. CMTC’s VeSM (Value energy Stream Map) tool was employed to identify various projects which would reduce costs, reduce delivery time and increase reliability of delivery time promises to customers.
Improvement Description
MCA Tile staff improved several areas of business operations as a result of the VeSM tool. The overall quality of the tile extruding and glazing operations was improved through training employees and applying Six Sigma quality process techniques. The company made significant gains in reducing tile warpage and color variation. MCA management was able to design, develop and implement a new computer scheduling system to improve scheduling of customer order delivery requirements against available plant capacity. A VeSM energy demand assessment of all plant equipment was conducted. This assessment resulted in improvement events which replaced some older, less energy efficient equipment with new advanced equipment to reduce on-going energy and product costs.
Financial and Investment Impact
The continuous improvement projects have resulted in improved quality, increased daily productivity and reduced product costs for MCA Tile. The quality and scheduling improvement projects have resulted in annual operating cost savings of $184,000. MCA invested $35,000 in new, more efficient equipment. The energy savings received from this equipment reduced annual energy consumption by 161,590 kWh saving $19,000 per year.
"CMTC has done an excellent job of helping us reduce costs and improve quality. We highly recommend their services.”
Yoshi Suzuki
CEO/President![]()
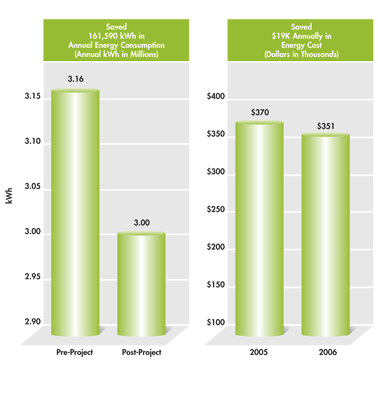
Case Studies
- Additive Manufacturing (3)
- Aerospace and Defense (14)
- Apparel (3)
- Business Growth Strategy & Strategic Planning (28)
- Continuous Improvement (8)
- Employee Training (14)
- Energy (7)
- Exporting (4)
- Farming (1)
- Food and Beverage (16)
- Fourth Industrial Revolution (24)
- Health & Safety Services (3)
- Industrial (1)
- Information Technology (3)
- Innovation & Growth (17)
- Lean (35)
- Machinery (1)
- Made in California (7)
- Manufacturing Technology (3)
- Medical (1)
- Plastics and Rubber (1)
- Quality (27)
- Sales and Marketing (32)
- Smart Manufacturing (1)
- Supply Chain Management (1)
- Wood (1)