Challenge
Packaging Plus LLC identified a need to improve performance through implementing lean manufacturing principles, reducing the amount of energy used per unit of output and transforming business processes. The majority of their products are categorized as made-to-stock, which results in a significant demand for raw materials, a high level of work-in-process and a significant amount of finished goods on hand. Packaging Plus LLC’s facility layout was overcrowded and the existing flow of products created manufacturing and energy use inefficiencies.Solution
With the assistance of Packaging Plus LLC, CMTC evaluated manufacturing processes and energy consumption by creating a current and future state Value Energy Stream Map; identifying several areas of improvement. CMTC scheduled 2 improvement events (Kaizens) that focused on 1) set-up reduction plant-wide and 2) 5S improvements in the Spyder assembly and packaging area. The project started in August 2005 and was completed in October 2005.
Improvement Description
Two separate week-long improvement events (Kaizens) were implemented. The first was set-up reduction using SMED (single exchange of die) approach plant-wide. Set-up reductions were implemented through documentation of standard operating procedures and training of operators. The second improvement event was implemented in the Spyder assembly and packaging area using 5S lean techniques (sort, set in order, shine, standardize, sustain) to improve throughput. After the two weeks implementation period, Packaging Plus LLC realized a reduction in set-up time, an increase in plant-wide productivity, a significant labor savings, a reduction in floor space through waste minimization and a more efficient use of energy.
Financial and Investment Impact
The impact of realizing a 50% reduction in set-up time plant-wide (4 hours to 2 hours) was a productivity improvement of 41% and a labor savings of $558,000 per year (three machines). Productivity improvement resulted in an annual reduction of 613,629 kilowatt hours, saving $61,000 (three machines on third shift did not need to produce to meet customer demand). The 5S improvement project in the Spyder assembly and packaging area produced a 27% productivity improvement and an 80 sq. ft. reduction in floor space.
“CMTC was able to show us how to use less energy in our operations and then they trained us how to do it ourselves.”
Scott Lilley
Director of Operations![]()
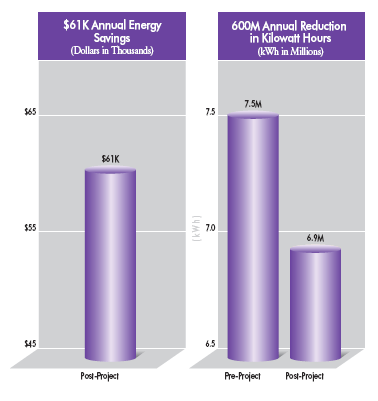
Case Studies
- Additive Manufacturing (3)
- Aerospace and Defense (14)
- Apparel (3)
- Business Growth Strategy & Strategic Planning (28)
- Continuous Improvement (8)
- Employee Training (14)
- Energy (7)
- Exporting (4)
- Farming (1)
- Food and Beverage (16)
- Fourth Industrial Revolution (24)
- Health & Safety Services (3)
- Industrial (1)
- Information Technology (3)
- Innovation & Growth (17)
- Lean (35)
- Machinery (1)
- Made in California (7)
- Manufacturing Technology (3)
- Medical (1)
- Plastics and Rubber (1)
- Quality (27)
- Sales and Marketing (32)
- Smart Manufacturing (1)
- Supply Chain Management (1)
- Wood (1)