Challenge
Two Chefs on a Roll had a steady track record of increased sales year after year. In late 2006, the company redefined their strategic goals to dramatically increase profit margins and market share over the next several years. They needed to reduce energy costs, improve operational efficiency and create a culture of continuous improvement in order to achieve their goals. They needed assistance in educating, training, and implementing initiatives to reduce cost and establish a culture of continuous improvement.Solution
In late 2006, CMTC’s food consulting group met with the executive team to discuss how they could assist the company in achieving their vision. The company agreed they needed a key person to be responsible for managing the initial and ongoing continuous improvement projects. CMTC assisted in recruiting an internal champion for their continuous improvement initiative. In addition, a Lean transformation plan was developed. Lean Transformation projects included basic Lean manufacturing concepts and simulation training for managers and employees, a Value energy Stream Map (VeSM) to identify energy savings opportunities in one of their Savory specialty food operation, Kaizen improvement events to reduce energy, production and inventory costs, and ISO 22000 assessment and implementation.Improvement Description
During the project, which started in January 2007, there was a total of over 300 hours of cross functional team facilitation by CMTC in Lean and continuous improvement techniques and principles. The Kaizen improvement event in the Savory processing area resulting in changeover/set- up reduction times from 22 to 8 minutes or 72% decrease in changeover time reducing energy consumption, increasing capacity and productivity by 15% while reducing rework and scrap. A second Kaizen event using the Lean tool of Total Productive Maintenance (TPM) resulted in increased equipment uptime of 80%. Company growth of 35% required the project to improve the plant layout resulting in increased efficiency and floor space reduction. Using Lean methodologies, the company increased inventory accuracy and developed the infrastructure required to support ISO 22000:2005 certification. The projected ended in May 2008.
Financial and Investment Impact
These improvements resulted in an annual cost savings of 28% as a result of a 4% increase in productivity, reduced energy consumption and increased capacity. These savings are in addition to the continuous improvement skills gained by the team members who worked on the different projects. The company has grown by 35% over the last two years adding 73 jobs.
"We highly recommend CMTC. Their training and assistance led to adaptation of Lean principles and sustained improvement."Eric Schmaranzer
Director, Supply Chain
and Continual Improvement![]()
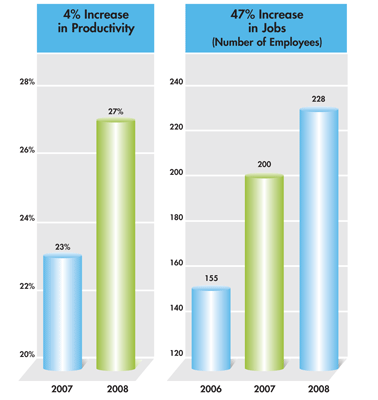
Case Studies
- Additive Manufacturing (3)
- Aerospace and Defense (14)
- Apparel (3)
- Business Growth Strategy & Strategic Planning (28)
- Continuous Improvement (8)
- Employee Training (14)
- Energy (7)
- Exporting (4)
- Farming (1)
- Food and Beverage (16)
- Fourth Industrial Revolution (24)
- Health & Safety Services (3)
- Industrial (1)
- Information Technology (3)
- Innovation & Growth (17)
- Lean (35)
- Machinery (1)
- Made in California (7)
- Manufacturing Technology (3)
- Medical (1)
- Plastics and Rubber (1)
- Quality (27)
- Sales and Marketing (32)
- Smart Manufacturing (1)
- Supply Chain Management (1)
- Wood (1)